7 July 2025
How to maintain electrical safety in the workplace
Electrical hazards pose serious risks in industrial and commercial settings, particularly where high-voltage equipment, complex installations or challenging environments are present. In a range of industries from manufacturing to energy, rail, and construction, even a momentary lapse in electrical safety can lead to severe injury or worse.
Protecting employees means taking a multi-pronged approach, combining technical controls, electrical safety rules, and appropriate workwear. Below, we explore essential steps for maintaining workplace electrical safety, from hazard awareness to regulatory compliance and protective clothing.
risk assessment and safe system design
Before any protective equipment is issued or work begins, employers must carry out a comprehensive risk assessment of all electrical systems. This means identifying hazards like exposed conductors, high fault currents, or inaccessible isolation points, and evaluating who could be harmed and how.
Under the Electricity at Work Regulations 1989, employers have a legal duty to ensure electrical systems are constructed and maintained so they do not pose danger. These regulations underpin the requirement for structured risk assessments and safe systems of work. From this, employers must develop technical controls such as physical barriers, signage, control panels and lockout protocols. Electrical zoning and equipment labelling further reduce confusion and error in high-pressure environments.
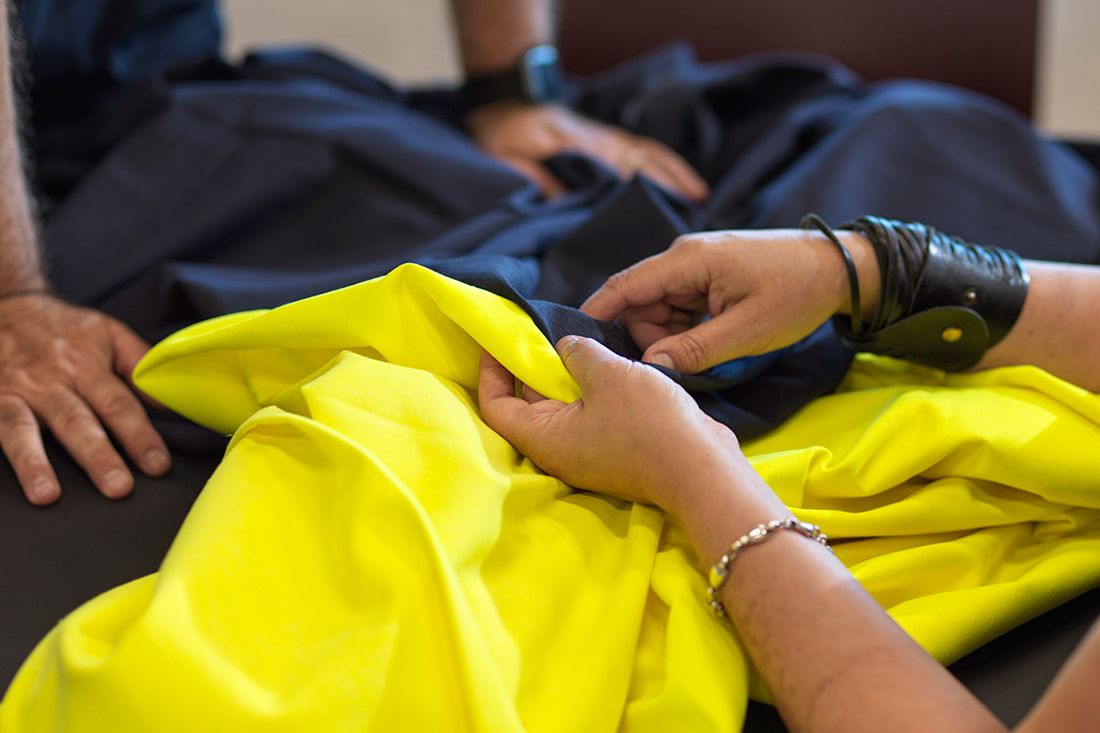
wearer protection
In high-risk roles, especially where equipment can’t always be de-energised, workers need clothing that can withstand extreme temperatures, UV radiation and thermal energy.
Arc-rated workwear – such as flame-retardant overalls, visors, gloves and footwear – forms a critical part of safe systems of work. All protective garments must be certified to relevant standards, including BS EN 61482 for arc flash protection.
Learn more about alsico’s range of arc flash clothing and electrical safety clothing for the electrification industry.
training
Even the best equipment cannot mitigate the many hazards of electricity without appropriate training. Workers who operate or work near electrical systems must understand how to identify risks, follow safe procedures, and use protective gear correctly.
Training should cover electrical isolation, lockout/tagout (LOTO), use of insulated tools, and emergency response protocols. It must be refreshed regularly and tailored to specific job roles. Supervisors and managers also need to know how to assess risks and enforce safety rules. Effective training not only reduces incidents, but also supports a broader culture of safety throughout the organisation.
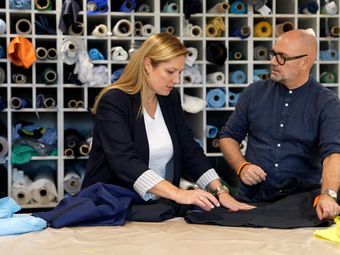
legal requirements and compliance
In the UK, electrical safety at work is governed by several key regulations. The Electricity at Work Regulations 1989 require all electrical systems to be constructed, maintained and operated safely. Regulation 14 specifically addresses work on or near live conductors and the precautions required.
Other relevant legislation includes the Health and Safety at Work Act 1974, which places a general duty on employers to protect workers from harm, and the PPE Regulations 2002, which mandate that suitable protective equipment must be provided where risks can’t be eliminated. Failing to comply can lead to prosecution, injury, or worse.
regular maintenance
Electrical safety isn't a one-off job. All systems require regular inspection and preventative maintenance to ensure continued safety and performance. This includes checking for worn insulation, corroded connectors, loose fittings, or thermal hotspots that may indicate overloads.
Maintenance records should be thorough and up to date, and any issues identified must be resolved promptly. Scheduled testing – such as Portable Appliance Testing (PAT) and thermal imaging – helps spot problems before they become dangerous. Neglecting routine maintenance doesn’t just create risk; it can also lead to costly downtime and breach of legal obligations.
common electrical hazards to watch for
Many incidents begin with basic issues that are easy to overlook. Awareness of everyday hazards is the first step toward prevention.
Some of the most common include:
- Faulty wiring: Exposed conductors, poor connections or DIY fixes can cause short circuits or arcing.
- Overloaded circuits: Too many devices drawing power from a single circuit increases fire and arc flash risks.
- Wet conditions: Water conducts electricity and can create fatal hazards in areas where equipment is exposed.
- Damaged insulation: Cracked or frayed insulation compromises protection, especially under load.
Routine inspections and hazard reporting can prevent these small issues from becoming serious failures.
keep employees safe with alsico workwear
Electrical safety in the workplace is not optional. It's an ongoing obligation for employers across all industries. It demands careful planning, diligent maintenance, appropriate workwear, and above all, informed and trained workers.
By addressing the common causes of electrical incidents and aligning with UK safety legislation, employers can significantly reduce the risk of injury or fatality. Alsico offers protective clothing solutions for environments where arc flash risks are present, helping your teams stay safe and compliant every day.
Contact our team for more information or to discuss your bespoke protective clothing requirements.
contact us