14 July 2025
What causes an arc flash?
Electrical accidents don’t always start with a fire or visible damage. Sometimes, the most devastating events come without warning, like arc flash. These violent electrical discharges can erupt in a split second, producing exceptionally high temperatures and causing life-changing injuries. Yet despite the risks, many workers still face arc flash exposure daily, often without fully understanding what causes it or how to reduce the danger.
This blog post breaks down the science behind arc flash, the conditions that trigger it, and the steps employers must take to keep people safe.
what is an arc flash?
Arc flash is one of the most dangerous electrical hazards in the workplace. It occurs when an electrical current travels through the air between conductors, generating a high-energy explosion of heat, light and pressure. The temperatures can exceed 19,000°C – hotter than the surface of the sun – instantly vaporising metal and causing life-threatening burns.
These events are sudden and violent, leaving little time to react. Workers in sectors like utilities, rail, construction, and manufacturing are particularly at risk.
For more information on what arc flash is and how to protect employees, make sure you read our guides to arc flash protection and arc flash PPE.
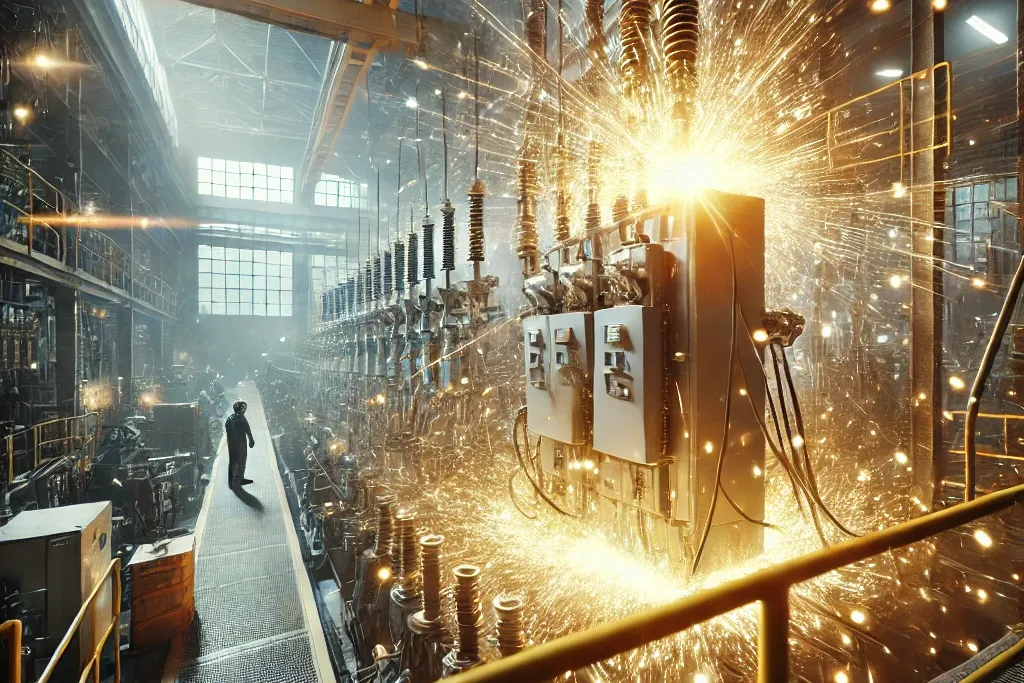
how do arc flashes happen?
Arc flash is typically the result of a fault in an electrical system, often a short circuit, where the current diverts from its intended path. There are several underlying common causes:
1. inadequate system design or modification
Arc flash hazards can be embedded into a system long before it's ever energised. Poor design decisions such as insufficient fault current analysis, improper protective device coordination, or tight spacing between conductors can all increase the risk of an arc incident. And when systems are modified without reviewing these factors, such as adding new loads or rerouting cables, the likelihood of fault conditions can grow unnoticed. Even something as simple as failing to update breaker settings after an upgrade can result in delayed trip times and greater incident energy.
Design should never be static; it must evolve with the system. Engaging qualified electrical engineers from the outset and after every major modification is critical to ensuring safety isn't compromised before a single switch is thrown.
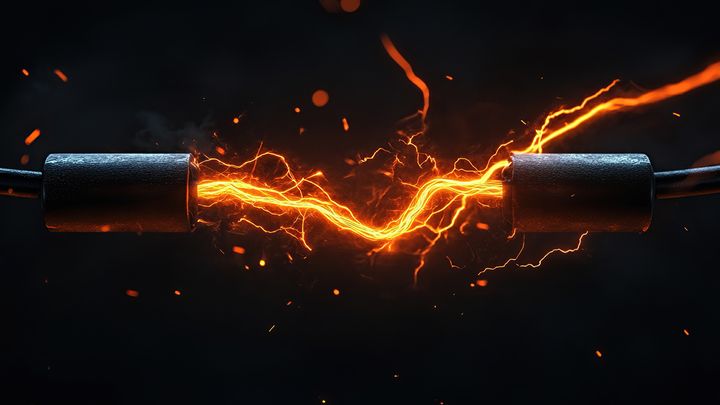
2. human error and unsafe work practices
Many arc flash incidents are caused by simple human mistakes. Contact with live parts, using uninsulated tools, or failing to isolate equipment correctly during maintenance can all trigger a fault. Inadequate training or rushing procedures can also often lead to bypassing lockout/tagout steps or working on energised equipment. Even skilled electricians can make critical errors under pressure or in poorly designed workspaces.
Employers must ensure that all personnel follow strict electrical safety protocols, and that no work takes place unless it is absolutely safe to proceed. Proper supervision, clear procedures, and a culture of hazard awareness all help reduce the human factor in arc flash risks.
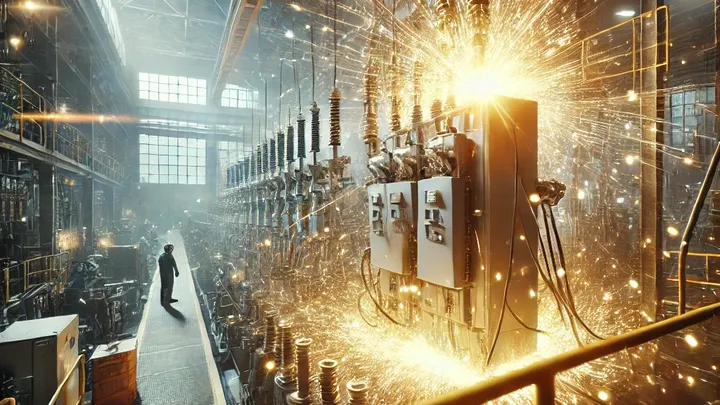
3. equipment failure/poor maintenance
Electrical systems degrade over time. Loose connections, worn insulation, aged switchgear or corroded terminals can all increase the likelihood of a fault developing into an arc flash. In some cases, equipment may not even be rated to handle the loads or conditions it’s exposed to (especially in harsh environments). Failing to inspect, clean or test electrical components regularly can allow these issues to go unnoticed until they result in a serious incident; preventative maintenance is therefore essential, as is investing in reliable components that meet the demands of the task.
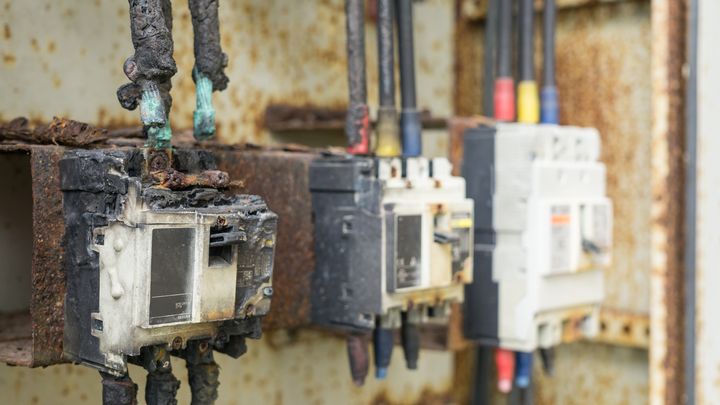
4. environmental causes (dust, moisture, foreign objects)
Not all arc flash incidents come from inside the system. External factors often contribute: dust build-up can become conductive and bridge electrical gaps, and high humidity or water ingress into enclosures can lead to unexpected current paths. Rodents, insects or tools accidentally left inside panels can also create faults.
These hazards are harder to predict but can be controlled through good housekeeping, sealing enclosures properly, and conducting thorough checks before energising equipment.
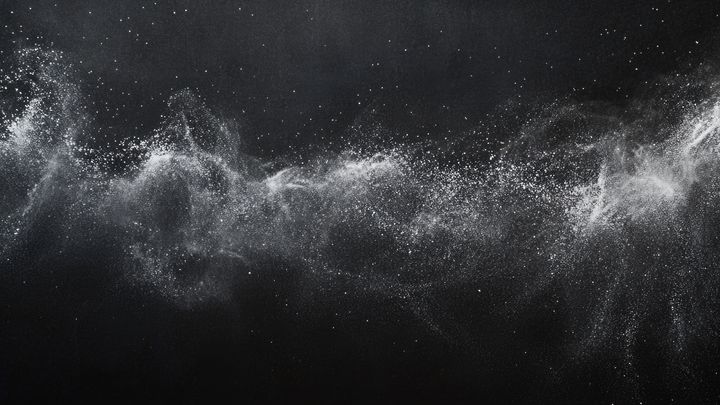
why arc-rated workwear is essential
Even with the best training and equipment, arc flash can still occur. That’s why arc flash garments are the last and most important line of defence to prevent or minimise arc flash injuries or deaths.
Arc-rated workwear is specifically designed to withstand the thermal energy and blast force generated by arc flash events. This includes flame-resistant coveralls, visors, arc flash hoods, gloves and dielectric boots. Each item must be rated for the incident energy level identified in your arc flash risk assessment. Workwear doesn't prevent the incident, but it can mean the difference between survivable injuries and a fatality.
trust alsico for arc flash clothing
Arc flash is fast, violent, and unforgiving, and for environments where electrical hazards are a daily reality, arc flash protection isn't optional – it's essential. Learn more about alsico’s solutions for electrical safety and explore our arc flash workwear range today, or contact our team for more information.
contact us